Written By – PKC Desk, Edited By – Rohit, Reviewed By – Balaji Prasath
Introduction:
DMAIC, an acronym for Define, Measure, Analyze, Improve, and Control, provides a structured framework within Six Sigma for refining existing processes. Each phase plays a crucial role in identifying issues, measuring performance metrics, analyzing root causes, implementing enhancements, and ensuring sustainable results. Let’s explore the significance of this acronym, its origins, evolution, effectiveness compared to other methodologies, criticisms, and why it remains a pivotal tool in industries globally.
Origins and Evolution:
The DMAIC methodology traces its roots back to Six Sigma, initially pioneered by Motorola in the 1980s. Developed as a response to manufacturing inefficiencies, Six Sigma aimed to minimize defects and variations in processes. DMAIC emerged within this framework as a systematic problem-solving methodology, gaining widespread adoption across industries for its effectiveness in driving continual improvement.
Evolution Over Time:
DMAIC has evolved beyond its manufacturing origins to encompass diverse sectors such as healthcare, finance, and services. Its adaptability and scalability have made it a preferred approach for addressing complex challenges in various organizational settings. Continuous refinement and integration with emerging technologies have further enhanced its applicability and effectiveness.
Aspects Under Each Phase of DMAIC
Define: In this phase, the project goals, scope, and stakeholders’ requirements are clearly outlined. Establishing a clear definition sets the foundation for successful project execution and ensures alignment with organizational objectives. Defining includes recognizing opportunities, define scope, create a value stream map and estimate a deadline for the project.
Measure: Measurement is crucial for understanding the current state of the process and identifying areas for improvement. Key performance indicators (KPIs) are defined, and data collection methods are established to quantify process performance accurately. Measuring include identifying the right data collection method, identifying the indicators, collect and examine data, etc.
Analyze: This phase involves analyzing collected data to identify root causes of issues or variations in process performance. Various analytical tools and techniques, such as root cause analysis and statistical analysis, are utilized to delve deeper into the underlying factors affecting process outcomes. Analyzing includes delving a root cause analysis, implementing process controls and
implementing initial plans and plans of improvement.
Improve: Based on the insights gained from the analysis phase, targeted improvement initiatives are implemented to address identified root causes and enhance process performance. Solutions are tested to ensure that they yield envisioned outcomes in the long run. Improvement includes identifying scenarios, testing them and improving solutions and processes based on the learnings made and feedbacks collected.
Control: After the initial pilot tests and subsequent user acceptance testing and improvement, now the process has to be made so that it sustains for a longer period of time. This includes identifying possible risk and deviation areas, setting quality standard, setting SOPs, etc.
Addressing Challenges Through DMAIC
DMAIC effectively addresses several common challenges faced by organizations:
Inefficiencies: By systematically identifying and eliminating process inefficiencies, DMAIC helps organizations streamline operations and enhance productivity.
Variability: DMAIC focuses on reducing process variability, leading to improved quality and consistency in outputs.
Customer Satisfaction: Through data-driven analysis and improvement initiatives, DMAIC enables organizations to better meet customer needs and expectations.
Waste Reduction: By targeting root causes of waste and inefficiency, DMAIC aids in reducing costs and optimizing resource utilization.
Sustainability: The Control phase of DMAIC ensures that improvements are sustained over time, preventing regression to previous performance levels.
DMAIC Versus Other Approaches
Compared to methodologies like PDCA (Plan-Do-Check-Act) or Lean Six Sigma, DMAIC offers a comprehensive framework with a strong emphasis on root cause analysis and sustainable solutions. Its structured approach and data-driven methodology make it particularly effective for addressing complex process improvement challenges.
Criticisms and Considerations
Despite its widespread adoption and effectiveness, DMAIC has faced criticism on several fronts:
Rigidity: Critics argue that the structured nature of DMAIC may limit creativity and innovation in problem-solving.
Lengthy Process: DMAIC’s five-phase structure may be perceived as time-consuming, particularly for organizations seeking quick fixes or immediate results.
Overemphasis on Data: While data-driven decision-making is a key aspect of DMAIC, critics suggest that excessive reliance on data may overlook qualitative factors and human judgment.
Conclusion
In conclusion, the DMAIC approach epitomizes disciplined and systematic process improvement, grounded in data-driven analysis and continual learning. Originating from Six Sigma, DMAIC has evolved to address diverse challenges across industries. While criticisms highlight the need for balance and flexibility, DMAIC remains a cornerstone in the pursuit of operational excellence. With its structured approach and emphasis on sustainable solutions, DMAIC continues to drive innovation and excellence in organizations worldwide.
As organizations continue to adapt to evolving market dynamics and customer expectations, the DMAIC approach stands as a timeless methodology for achieving operational excellence and driving continual improvement. Its structured framework, coupled with a focus on data-driven decision-making, empowers organizations to navigate complex challenges and achieve sustainable success in today’s dynamic business landscape.
Author
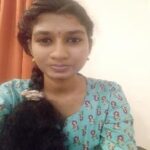
Sneha K