Written By – PKC Desk, Edited By – Abinesh, Reviewed By – Balaji Prasad
Sustained success in today’s world rests on the ability of a business to adapt, innovate, and evolve. It demands transformation, and not just incremental changes. That’s where business process reengineering (BPR) comes into play.
BPR is not just about tweaking existing traditional systems, rather, it is about revolutionizing them to foster unprecedented business innovation and efficiency. Learn with us the foundations of this business transformation with BPR.
What is Business Process Reengineering?
Business Process Reengineering (BPR) is a strategy focused on radical redesign of business processes to achieve substantial performance, quality and productivity improvements.
It is not merely about making small adjustments; it is a mindset shift that aims to fundamentally transform how businesses operate.
Introduced in the 1990s by Michael Hammer and James Champy, BPR advocates starting from a “clean slate.” It involves a fundamental rethinking of how work is done to streamline processes, eliminate redundancies, and leverage technology to achieve breakthrough results.
Core Principles of Business Process Reengineering
- Innovation is Imperative
Innovation drives business success. BPR sparks innovation by rethinking workflows, removing barriers, and creating space for new ideas that help businesses stay ahead..
- Identifying Bottlenecks and Inefficiencies
BPR starts with analyzing current processes to find inefficiencies. Addressing these issues clears the path for innovation and lasting improvements.
- Encouraging Cross – Functional Collaboration
Innovation grows through diverse input. BPR breaks down silos, boosting collaboration and communication across teams to fuel fresh ideas.
- Embracing Technology as an Enabler
BPR leverages technology to streamline tasks and spark innovation. Smart tech use boosts efficiency and uncovers new opportunities.
- Cultivating a Culture of Continuous Improvement
BPR is ongoing. A culture of constant feedback, adaptability, and experimentation keeps innovation alive and processes evolving.
How is Business Process Reengineering (BPR) Different from Business Process Engineering (BPE)
BPR and BPE are related concepts but differ in their approach and scope:
Focus & Scope:
- BPR involves radically redesigning existing processes from scratch to achieve dramatic efficiency gains that often disrupt traditional workflows.
- BPE focuses on systematically designing or optimizing processes using engineering principles, often focussed on new systems or incremental improvements.
Approach:
- BPR is transformational, prioritizing revolutionary change e.g., eliminating outdated steps, leveraging technology and the like.
- BPE is methodical, emphasizing technical modeling, standardization, and structured problem-solving.
Purpose:
- BPR aims to overhaul processes for breakthrough outcomes (e.g., cost reduction, customer satisfaction).
- BPE seeks to create or refine processes to align with organizational goals, ensuring reliability and scalability.
Outcome:
- BPR targets high-risk, high-reward results.
- BPE delivers controlled, predictable enhancements.
Metric | Before BPR | After BPR |
Process Time | Manual approval workflows with multiple handoffs | Automated workflows with single-point ownership |
Operational Costs | High labor and overhead costs | Streamlined processes with automation |
Error Rates | Error-prone manual data entry | AI-driven validation and standardization |
Customer Satisfaction | Slow response times | Real-time tracking and self-service portals |
Employee Productivity | Siloed teams with redundant tasks | Cross-functional roles with automation |
Compliance & Risk | Ad-hoc audits and compliance gaps | Automated compliance checks |
Innovation Rate | Slow adoption of new tools | Agile workflows and rapid prototyping |
Benefits of Business Process Reengineering for Modern Organizations
- Enhancing Operational Efficiency: Eliminates unnecessary steps and streamlines workflows through automation, enabling faster output. Helps align roles and systems to reduce delays and bottlenecks.
- Cost Reduction and Resource Optimization: Identifies and eliminates non-value-adding activities, reducing operational waste and overhead costs. Optimizes resource allocation to maximize ROI while maintaining quality.
- Fostering Innovation and Competitive Advantage: Encourages radical rethinking of processes, promoting creative solutions and differentiation in the market. Enables quick responses to industry trends.
- Improved Customer Satisfaction and Experience: Aligns processes with customer expectations boosting loyalty. Reduces errors and delays, ensuring consistent, high-quality service experience.
- Better Risk Management and Compliance: Standardizes processes to minimize errors and ensure regulatory compliance. This reduces legal/financial risks.
- Cultural Transformation and Employee Empowerment: Breaks down silos and encourages collaboration, enabling continuous improvement. Empowers employees with decision-making authority and cross-functional skills, boosting engagement.
- Scalability and Future-readiness: Designs flexible processes that adapt to growth, market shifts, or technological advancements. Lays a foundation for integrating emerging tools (e.g., AI, analytics) to stay competitive long-term.
Business Process Reengineering Methodology: Step-by-Step Approach
Step 1: Identifying and Analyzing Existing Business Processes
The main objective here is to map and evaluate current workflows to pinpoint inefficiencies, redundancies, and bottlenecks.
Activities:
- Process mapping: Document how tasks are currently performed, who performs them, and in what sequence.
- Data collection: Gather performance metrics -time, cost, errors, customer satisfaction.
- Identify pain points: Highlight inefficiencies, redundancies, delays, or quality issues.
- Stakeholder interviews: Gain insights from employees, managers, and customers on problems and improvement opportunities.
Step 2: Redesigning Processes for Maximum Impact
The aim is to create a “to-be” process model that eliminates waste and utilises technology for transformative outcomes.
Activities:
- Define goals: Establish what the redesign should achieve e.g., faster delivery, lower costs, improved quality.
- Brainstorm solutions: Use creative thinking, benchmarking, and technology to find better ways to achieve the objectives.
- Leverage technology: Incorporate automation, digital tools, or AI where applicable.
- Redesign workflows: Reconfigure steps, roles, and responsibilities to eliminate non-value-adding activities.
- Risk analysis: Anticipate obstacles or unintended consequences of new designs.
Step 3: Implementing Change and Managing Transformation
Next step is to execute redesigned processes while addressing resistance and ensuring stakeholder buy-in with minimal disruption.
Activities:
- Develop an implementation plan: Outline resources, timelines, tasks, and responsibilities.
- Communicate change: Ensure all stakeholders understand the changes and the reasons behind them.
- Train employees: Equip teams with skills and knowledge to work within the redesigned processes.
- Pilot testing: Run small-scale trials to validate the redesign before full rollout.
- Change management: Address resistance, encourage buy-in, and support cultural adaptation.
Step 4: Monitoring, Measuring, and Continuous Improvement
Track post-implementation performance and refine processes based on feedback.
Activities:
- Performance tracking: Measure key metrics like time, cost, quality, and customer satisfaction.
- Feedback mechanisms: Collect feedback from users and customers to identify issues.
- Benchmarking: Compare against internal targets and industry standards.
- Process audits: Periodically review processes to ensure compliance and efficiency.
- Continuous improvement: Use tools like Six Sigma, Kaizen, or Lean to make incremental improvements.
Successful Business Process Reengineering: Ford Motor Company BPR Case Study
Ford Motor Company is often cited among the pioneers of BPR.
In the late 1980s, facing financial struggles and increasing competition, Ford embarked on a major restructuring effort aimed at reengineering its manufacturing processes under the leadership of then-CEO Harold “Red” Poling.
They focused on implementing just-in-time manufacturing, total quality management, and flattening the organizational hierarchy.
Below are the key aspects of the BPR of Ford Motor Company
- Just-In-Time Manufacturing: Ford implemented the concept of just-in-time manufacturing, inspired by Japanese methodologies like Toyota’s lean production system. This reengineering of the manufacturing process focused on reducing inventory and waste by receiving parts only as and when they were needed in the production process. It minimized storage costs and improved efficiency.
- Total Quality Management: BPR at Ford emphasized TQM principles, aiming to enhance quality at every stage of production. This involved a cultural shift across the company, focusing on continuous improvement, reducing defects, and involving employees at all levels in quality control.
- Flattening the Organizational Hierarchy: Ford flattened its organizational structure, streamlining decision-making processes and empowering employees at various levels to contribute ideas and improvements. Encouraging effective communication resulted in a more agile and responsive organization, enabling quicker adaptation to market demands.
- Advanced Manufacturing Technologies: Ford invested in and implemented advanced manufacturing technologies to automate and optimize production processes. This included robotics, computer-aided design (CAD), and computer-aided manufacturing (CAM) systems to improve precision and efficiency in car manufacturing.
- Supplier Relationships and Partnerships: Ford reengineered its relationships with suppliers, establishing long-term partnerships and focusing on collaboration rather than mere transactional interactions. This streamlined the supply chain, ensuring high-quality parts arrived on time, reducing delays and costs.
- Product Development Process: Ford reengineered its product development processes, emphasizing cross-functional collaboration among design, engineering, and production teams. This resulted in shorter product development cycles and faster time-to-market for new models.
These BPR initiatives at Ford aimed to overhaul its operations comprehensively, aligning them with modern methodologies and best practices.
This shift in mindset and processes allowed Ford to significantly improve its operational efficiency, product quality, and competitiveness in the automotive industry, marking a crucial phase in the company’s history of innovation and adaptation.
Overcoming Challenges in Business Process Reengineering Initiatives
Significant BPR challenges can arise in organisations that may impact its success. Here are a few challenges and their solutions:
Employee and Stakeholder Resistance to Change
To tackle this, encourage stakeholder buy-in through transparent communication and early involvement of employees. Highlight benefits and address fears through training and support.
Lack of Leadership Alignment
Secure executive sponsorship to drive vision and allocate resources. Leaders must set an example of commitment and empower cross-functional teams to own the redesign.
Unclear Goals and Scope Creep
Define SMART (Specific, Measurable, Achievable, Relevant, and Time-bound) goals upfront and prioritize high-impact processes. Use tools like value stream mapping to stay focused on critical areas and avoid over complications.
Legacy Systems and Technology Gaps
Invest in scalable, modern tools like automation and AI, and phase out outdated systems. Pilot-test integrations to ensure compatibility and minimize disruption.
Internal Competencies and Minimal Expertise
Upskill employees through targeted training. Partner with external consultants like PKC Management Consulting for specialized knowledge. Build a culture of continuous learning.
Inadequate Measurement and Feedback
Track KPIs (e.g., cycle time, cost savings, profit margin,) post-implementation. Adopt iterative improvement frameworks like PDCA (Plan-Do-Check-Act) to refine processes.
Cultural Inertia
Encourage collaboration and reward innovation. Align incentives with BPR outcomes to reinforce new behaviors.
Best Practices for Effective Business Process Reengineering
BPR success hinges on balancing innovation with planned execution. Here’s a look at some of the BPR best practices that can help:
Secure Leadership Commitment
Ensure top executives back the initiative, providing vision, resources, and authority to drive the transformative changes. Leaders must assure accountability and resolve conflicts.
Align with Strategic Goals
Link BPR objectives to overarching business goals such as growth, customer retention, etc. to ensure efforts deliver measurable, mission-critical outcomes.
Understand and Analyze Existing Processes
Document and map current workflows to identify inefficiencies, redundancies, and bottlenecks. Use data and performance metrics to drive decision-making.
Engage Cross-Functional Teams
Involve employees from all impacted departments to break silos, gather diverse insights, and foster ownership of new workflows.
Leverage Technology
Use automation in business such as AI, or cloud tools to enable radical improvements. Incremental tweaks are not enough to observe transformative changes.
Use Data-Driven Insights
Base decisions on quantitative metrics and KPIs to identify inefficiencies and validate redesign effectiveness.
Adopt a Clean-Slate Approach
Challenge assumptions by redesigning processes from scratch rather than tweaking existing systems. Ask: “If we were starting today, what would we do?”
Prioritize Communication & Training
Address resistance to change through transparent communication, regular updates, and skill-building programs to ease transitions.
Document Processes Rigorously
Map “as-is” and “to-be” workflows in detail to clarify roles, dependencies, and expectations for stakeholders.
Manage Risks Proactively
Anticipate risks (e.g., system failures, employee pushback) and develop mitigation plans (e.g., contingency budgets, change champions).
Celebrate Wins
Highlight early successes (e.g., reduced processing time) to maintain momentum and reinforce the value of BPR efforts.
Future of Business Process Reengineering: Trends and Innovations
The future of BPR is being molded by digital transformation and emerging technologies. Some of the key trends and innovations include:
1. AI-Driven Process Automation and Intelligence
AI is enabling systems to learn, adapt, and make decisions without human intervention. This leads to smart, responsive processes that quickly adapt to business and customer needs.
AI-driven automation can:
- Predict process bottlenecks and recommend solutions.
- Automatically adjust workflows in real-time based on data.
- Understand and process natural language, images, and unstructured data.
2. Hyper Automation (RPA + AI + Process Mining)
Hyper Automation refers to the completing use of multiple technologies—particularly:
- Robotic Process Automation (RPA) for repetitive tasks,
- AI and Machine Learning for cognitive decision-making, and
- Process Mining to uncover inefficiencies and real workflows.
Together, they help organizations fully automate and optimize end-to-end processes delivering faster, more accurate, and cost-effective outcomes.
3. Cloud-Native and Decentralized Process Architectures
BPR today is increasingly relying on cloud-native architectures. These are:
- Scalable – grow with business needs.
- Flexible – support remote work and global teams.
- Integrative- easily connecting with APIs, IoT, and enterprise apps.
Decentralization allows process components to run across multiple environments, improving reliability, collaboration, and innovation.
4. Customer-Centric Redesign
BPR is shifting from being efficiency-based to experience-based. This approach puts customer at the center of all process decisions:
- Mapping touchpoints to identify pain points.
- Reengineering processes to ensure consistency across channels.
- Using customer feedback and data to continuously enhance service.
The goal is to align internal workflows with customer expectations, improving satisfaction, loyalty, and lifetime value.
5. Human-AI Collaboration in Process Design
Rather than replacing humans, future BPR will enhance human capabilities with AI:
- Co-designing workflows with AI assistance
- Real-time decision support for employees
- Empowering employees to use low-code/no-code platforms to tweak or build processes.
This enhances a collaborative environment where humans and machines work together to design, monitor, and evolve business processes.
6. Continuous Evolution via Digital Twins
Digital Twins of processes are virtual replicas that simulate, monitor, and optimize real-world operations. With them, organizations can:
- Test process changes in a risk-free virtual environment.
- Monitor performance in real-time using live data feeds.
- Forecast outcomes and dynamically improve processes.
This innovation shifts BPR from being a one-time transformation to a continuous, real-time improvement cycle, boosting adaptability and resilience.
Get In Touch With Our BPR Experts Today!
Frequently Asked Questions about Business Process Reengineering
- What is the main goal of business process reengineering?
The main goal of BPR is to radically redesign core business processes to achieve substantial improvements in performance—such as cost reduction, quality enhancement, speed, and customer satisfaction.
- How does BPR drive innovation and business growth?
BPR fosters innovation by challenging outdated assumptions and leveraging new technologies like AI, automation, and cloud computing. This can help in creation of more agile and responsive processes, enhanced customer experience and faster time-to-market for products and services.
- What are the key steps in a successful BPR project?
The key steps include:
Step 1: Identifying and Analyzing Existing Business Processes
Step 2: Redesigning Processes for Maximum Impact
Step 3: Implementing Change and Managing Transformation
Step 4: Monitoring, Measuring, and Continuous Improvement
- What industries benefit most from business process reengineering?
While any industry can benefit, BPR is particularly impactful in sectors where efficiency, speed, and customer experience are critical, such as Manufacturing, Retail & E-commerce, Healthcare and Banking & Finance.
- How can organizations overcome resistance to BPR initiatives?
Resistance to BPR often arises from fear of change, job insecurity, or lack of understanding. Organizations can address this by communicating clearly and consistently about the goals and benefits of BPR, actively involving employees, and providing training and support.
Author
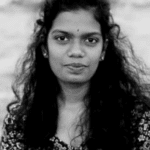
Deepa Naganathan
I am a dedicated lifelong learner with a profound passion for reading, continuously seeking to broaden my knowledge with practically applying the theoritcal knowledge to solve business problems.